The launch of the new Active Photothermal Camera (APC) is near. So, despite the current circumstances (COVID-19), we remain mobilised because we are keen to share with you the advances made on this product. After telling you about its very promising results and its new design, we talk to you today about the future NDT software that will accompany the new CPA.
We interviewed 3 expert users who have been working on this project since the beginning and who have therefore experienced the evolution of CPA and especially its software:
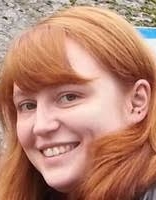
Axelle ELRIKH
R&D methods engineer at Framatome Intercontrôle
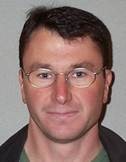
Stéphane BOURGOIS
NDT methods technician at Framatome
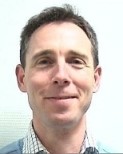
Yannick CAULIER
NDT methods expert at Framatome
Below is a summary of their answers to our questions as well as their comments, which we will use to optimise our future NDT software.
Can you tell us about the current software used with CPA: main function(s), strong point(s), improvement point(s)?
The main function of this software is to control the complete acquisition and analysis chain of the CPA. To do this, it controls the laser and the camera, it records the data and it restores a thermographic image of the studied piece after the inspection. The use of measurement and filtering tools allows the signal to be improved.
The strong point of the software is its ability to control both the laser (power, speed of movement, line quality) and the camera as well as a rotation axis. And of course, it allows the result to be delivered.
The first point to be improved would be the signal acquisition and processing. The signals as presented are not sufficiently processed to be presented directly to a neophyte and the quality of the images could be better. It is still a specialist tool whose ergonomics, handling and robustness need to be improved. The current software is not adapted to the use of a product on a shelf.
The second point to be improved would be to obtain a reporting tool that is simple and intuitive to use. This is a big point to improve for future users.
The last point to be improved would be the calibration / verification part. With the current software, this is a source of error because there are a lot of verifications which are done in 2 or even 3 steps whereas 2 clicks should be enough. The ergonomics, the speed (a few clicks) to check that the system is well adjusted, that you have the right power, the right line width, that the pixel / laser line offset is good, etc., are all important factors. All these elements must be easy to implement and check. Overall, the inspection must be simplified in order to obtain the result in just one click, with the processed image displayed without too many modifications, so that the user can see directly where the notorious and non-notorious indications are.
Since the beginning of our collaboration project, you have had the opportunity to see or use the NDT software of Edevis DisplayIMG 7 (DI7), what did you think? What do you like about this software?
First of all, the NDT software is much easier to use. They had the intelligence to take over the Windows interface, so right away it’s very instinctive. In no time at all, I managed to use it, make reports, process images, put them in the right format, place tools, integrate images into reports, etc. The NDT software integrates all these little functions that are quite obvious today and which, when you don’t have them, make everything more complicated. It is possible to manipulate signals, to drag and drop. They also have many more signal processing options and that’s what we really lacked with the current software. We can apply many more filters which are very interesting. We can make measurements with ROI tools (distance, surface, etc.), other than a simple frame. We can do signal averaging. We can put several signals on the same thermal image. Many small things that we didn’t have and that make the difference. Because of its conception, it is already much more developed than the software we have at the moment.
What do you think is DI7’s strong point?
I would like to start by pointing out that CPA remains an expert tool that needs to be handled by trained users. On the one hand, for the safety side, which is very important, and on the other hand, for the understanding side, which is also important in order to understand the signals that we are going to get. For example, in the CPA’s flagship case, which is the inspection of Pelton wheels, a minimum level of warning is required to be able to distinguish between essential and non-essential defects. This means that, even if the user has to be an expert in the CPA technique, it is still necessary to have a software that can be handled fairly quickly. This is the case with Edevis’ DI7 NDT software. It has been designed to be, above all, a software for the operator and not for experts.
What do you absolutely expect from the future NDT software and what would be the indispensable improvements to be made to make it marketable and adapted to the target audience?
I am simply waiting for it to respond in every point to the spec that has been written. But the point that Edevis still needs to work on is everything they didn’t know before: CPA and laser line adjustment. This is the most important point and I know that Edevis’ engineers are working on it. This is a key parameter of the NDT software corresponding to a virtual pixel line set to the real physical laser line. It is purely software but it is not that simple to implement. On the current software, you can position the pixel line on the laser line, you can make this adjustment. This also allows us to check and measure the homogeneity of the laser line. It’s very important for us to be able to have our hand on the positioning of the line because it will condition the whole acquisition. If we want to deliberately put an offset or simply check that it is well aligned, this can be useful to us. Finally, it’s almost like a preliminary calibration for any acquisition which allows us to check that the 2 lines are well aligned. It is on this point that we will wait the most for Edevis around the corner because we know that for the rest, they will know how to do everything.
On the other hand, when we do serial acquisitions on site, the reports are done by hand and we sometimes get lost when we do 25 acquisitions in one day. It’s sometimes difficult not to get confused. So if we had an automatic report, it would make things much simpler right away.
Finally, it is important that at each stage, and especially in the current validation phase, the operators are put in the loop so that they can use the software and make their returns. This is very, very important because in the end they are the future operators on site. Never forget for whom this software will be made.
Thanks to Axelle, Stéphane and Yannick for their remarks and advices which will be taken into account in the future version of the NDT software that we will make you discover soon.
Video illustrating the operation of the NDT software
Example of processing on two easily detectable defects
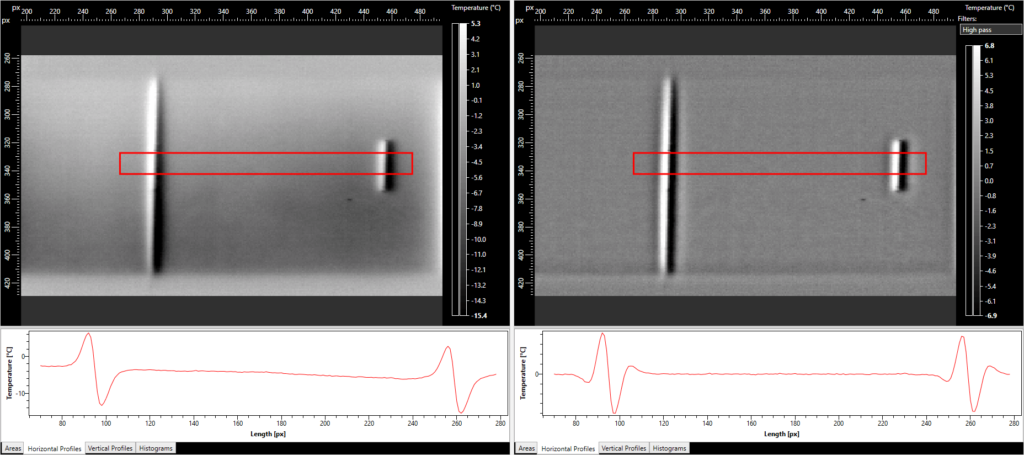
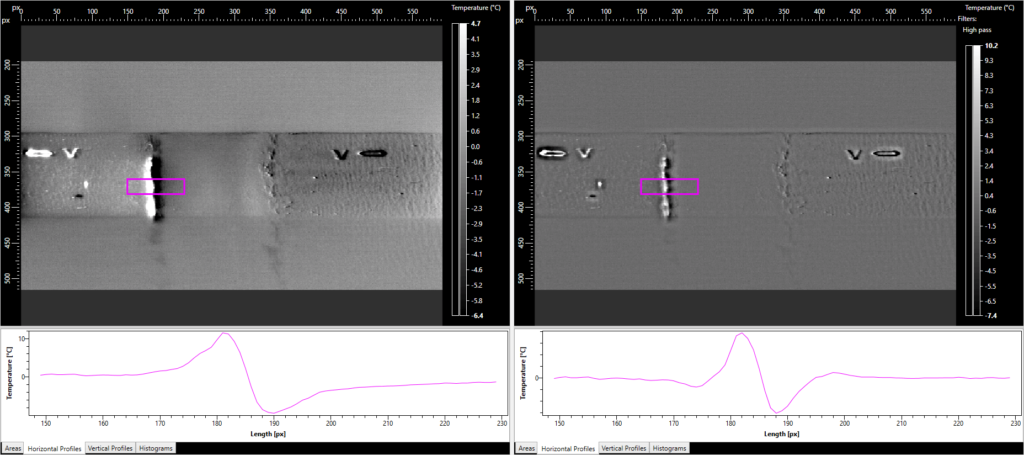
On the left, results before processing / On the right, results after processing
In the case of very marked defects, the bipolar signal which serves as a detectability criterion is already present before the processing (see curves under the infrared images on the left above), but the processing applied allows the signal to be normalised and accentuated, making it more easily detectable.
Example of processing on two hardly detectable defects
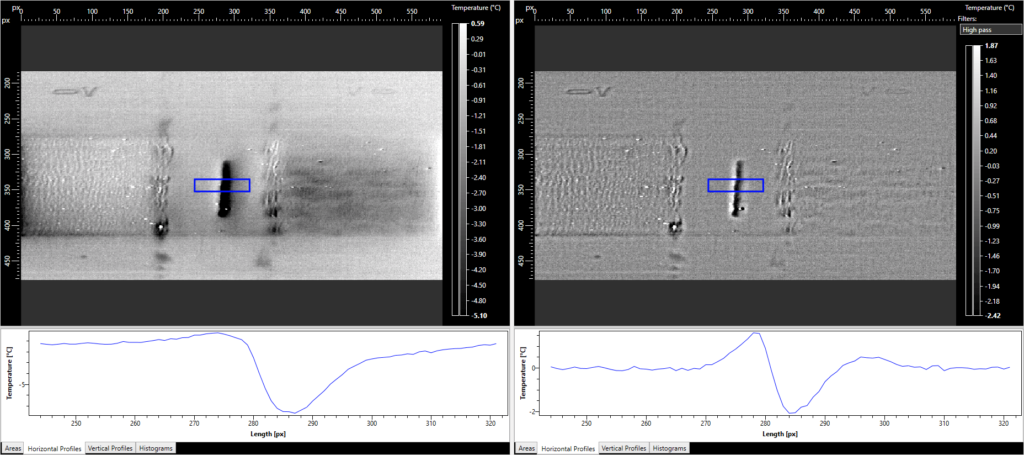
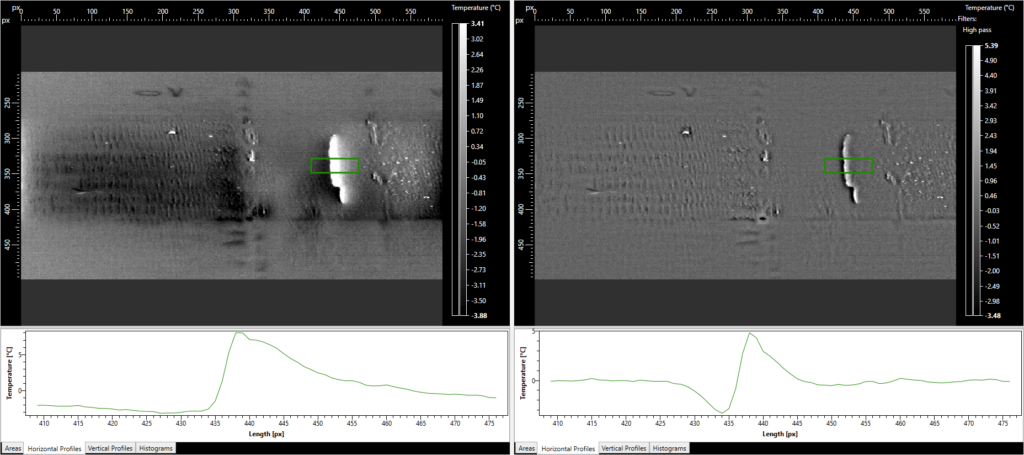
On the left, results before processing / On the right, results after processing
On the above defects, without processing it is impossible to detect the defect or to separate it from the healthy environment. Thanks to the image quality obtained and the processing used, the bipolar characteristic signal is immediately identifiable, making the defect instantly detectable. This makes it possible to consider an automatic sanctioning of defects.
Soon new information will be communicated to you about this product before its official launch in June 2020.
Stay tuned to the LinkedIn account of our NDT expert, Richard HUILLERY, to discover very soon the final visual and the new name of the CPA!
Do not hesitate to contact us if you have any questions about this article or to discuss this system either by the website contact form or by phone at +33 (0)5 47 74 62 12.
Recent Comments